If you have recently purchased a laser foam cutting machine? It so happens that you are still new to laser cut foam. Then you might want to ask for some cautions.
You may have heard stories that some foam or certain laser types can cause the machine to catch on fire. Maybe it’s because of the gases emitted by laser cut foam? Maybe those machines are not well ventilated? What can cause a laser cutter to catch fire while cutting foam?
Most materials are prone to fires. Almost anything flammable can catch fire. For example, you can also catch fire when cutting plywood, paper, or cards. Most materials depend on the setup, in any case. We can cut a small sample, see what it does, and then adjust your settings accordingly.

How to laser cut foam?
If you want to laser cut foam or adhesives with a laser foam cutting machine for a long time. Then they must be treated in a different way than engraving wood or metal. The first and most important thing is to use an excellent air-assist device and vacuum the fumes out of the machine. And filter the foam, preferably before cleaning. This way, the laser cut EVA foam will not stick. Remember that it is before the laser cut EVA foam comes into contact with outside air.
Laser cut eva foam
To maximize the effect of complete air assist, lower the laser nozzle to 3 mm from the surface. Reduce the heat entering the work by using point mode, low power, and low speed. To make dimensionally correct holes (-ve value slit) and plugs (+ve value slit), experiment with different slit offset values.
The actual figures are determined by the type of laser cut foam utilized, thickness, density, and laser power. I usually set the power at 18% (around 20 watts) / speed 6 mm/sec / perforation for 30 mm thick polyethylene (PE) foam. 0.3 / notch offset 1.25 / perforation skip 0.2 You’ll need a point setting of 0.05 sec / 0.2 mm point interval / 0.3 mm point length. Each substance has its qualities that influence how the laser beam interacts with it and hence affect it.
The following are the most frequent foam treatment methods:
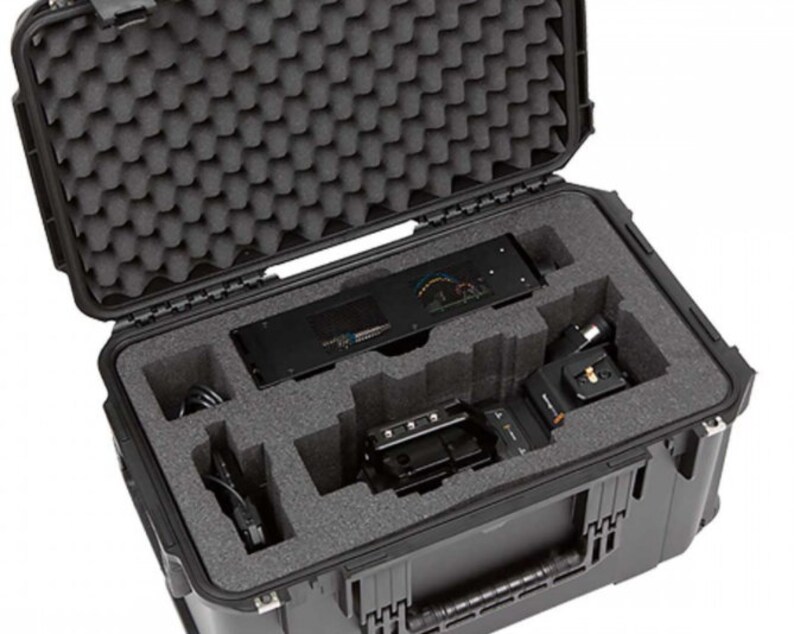
Laser cutting foam polymer-based foams
A CO2 laser can efficiently cut this type of foam. The laser beam heats the material that it passes through, causing it to evaporate. The laser beam will cut entirely through the material if the laser strength is high enough.
When the polymer is sliced with a laser beam, it evaporates quickly, leaving smooth edges with little heat impacted zone. Fiber lasers are the most effective for metal-based foams. Fiber lasers can easily cut thin foam sheets (up to 1/8 inch or 3 mm). Lasers are rarely used to cut ceramic-based foams since they are brittle and easily shatter.

Best foam for laser cutting
Metal foams are well suited to fiber optic lasers. The laser cut foam board can limit the laser beam’s power to remove the material (engraving) to a specific depth. Laser etching of polymer foam is best done with a CO2 laser. On the surface of the foam, you can utilize the laser engraving process to create patterns and designs.

Ceramic Foams
Laser marking of metallic and ceramic foams is possible with a fiber laser. This laser cut foam board will leave a visible mark without removing the material. The fiber laser beam’s energy is absorbed by the material’s surface, causing it to warm up and alter color or tone.
Combined laser cut foam core process
The previous laser cutting, engraving, and marking procedures can combine without relocating or re-fixing the foam.
Precautions for laser cut foam
Platform size
the size that can hold laser cut foam. And equipped with 4 levels of capability and safety precautions to laser cut foam board.
Wavelength
The optimal wavelength for laser cutting and engraving polymer foams is 10.6 microns. The ideal wavelength for cutting, engraving, and branding metal foams is 1.06 micron. Laser marking ceramic foams with a wavelength of 1.06 micron is also a popular option.
Laser power
It would help if you were chosen based on the procedure to be carried out. Metal or ceramic foam laser processing is best done with a 40 to 50 watt fiber laser. A CO 2 laser with a power range of 25 to 150 watts is ideal for polymer foam laser processing.
Lenses
The best universal process lenses for processing foam laser materials are 2.0 lenses.
Cutting Table
Supports laser cut foam sheets.
Air Exhaust
During the laser operation, there must be enough flow to remove gases and particles generated by the foam laser engraving, cutting, and marking equipment.
Air Assist
Air jets are placed near the laser focus to remove gases and particles generated during the foam laser engraving, cutting, and marking process.
Which foams are safe for laser cutting?
Foams made from polyester (PES), polyethylene (PE), and polyurethane (PUR) are ideal for laser cutting, engraving and marking.
What materials are not safe to cut?
- Vinyl and Pleather are examples of PVC (emits chlorine gas)
- ABS (emits cyanide gas)
- Carbon fibers with a coating
- Laser light-reflective materials (chrome or copper)
- Polypropylene or polystyrene foam
- Fiberglass
- Milk bottle plastic (HDPE)
Safety precautions for laser cut foam

When a laser interacts with a substance, gaseous effluents and particles are virtually always produced. Laser cut foam manufacturing effluent will contain volatile organic compounds (VOCs) and should be disposed of outdoors. It can also be processed using a filtration system before being sent to the outside world. Laser processing causes foam combustion, which can result in flames. As a result, people must monitor the foam laser material processing process.
The process of laser cutting foam
- When cutting any new material, particularly foam material. You must ensure that the laser foam cutting machine is configured correctly.
- Using the laser program of your choice, create a 25-mm test square using PE foam, PUR foam, or PES foam. Then choose a point mode or a laser processing mode that is equal.
a. You’ll need more power or a slower speed if your foam is denser.
b. You’ll need less power or a faster speed if your foam is thinner. - Use your longest focal lens, preferably 2.5″ or 4″. However, if you only have a 2″ lens, you may still cut it.
- Prepare your machine for the material.
- Position the laser nozzle about 3mm from the foam surface for foams less than 10mm thick. This may not be necessary.
- Repeat the 25 mm square test until you obtain a cut that is as vertical as possible, with no taper.
Applications for laser cut foam
The main application of laser cut foam may be foam inserts for toolboxes. Foam can become extreme very quickly, but you should not be afraid to use it because it has many uses. The maximum power of the laser during the cutting process is cut as fast as possible. In addition, foam is not a material that will reduce your safety, so please be aware of it throughout the cutting process.